bussiness
Financial &Budget Management
"Maximizing Efficiency and Performance Through Strategic Process Optimization"
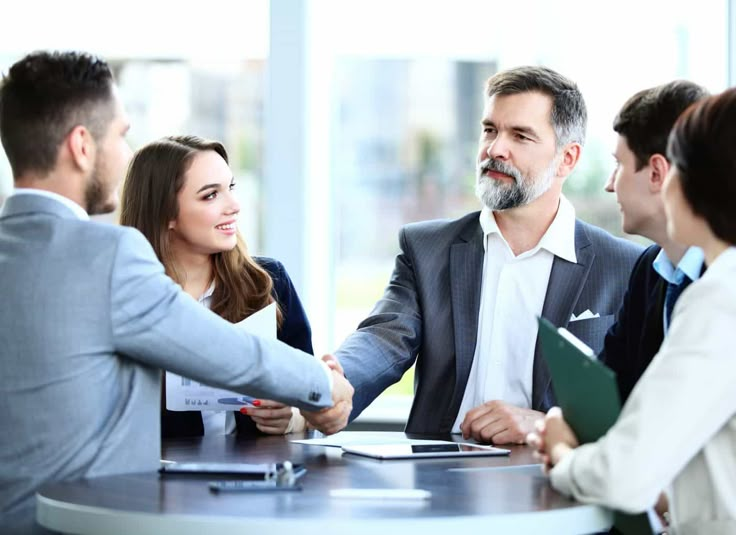
Strategic Planning & Risk Management
Read More
We help organizations make informed decisions through strategic planning, accurate financial forecasting, and comprehensive risk assessment. Our approach ensures you’re prepared for uncertainties, aligned with goals, and positioned for stable, long-term success.
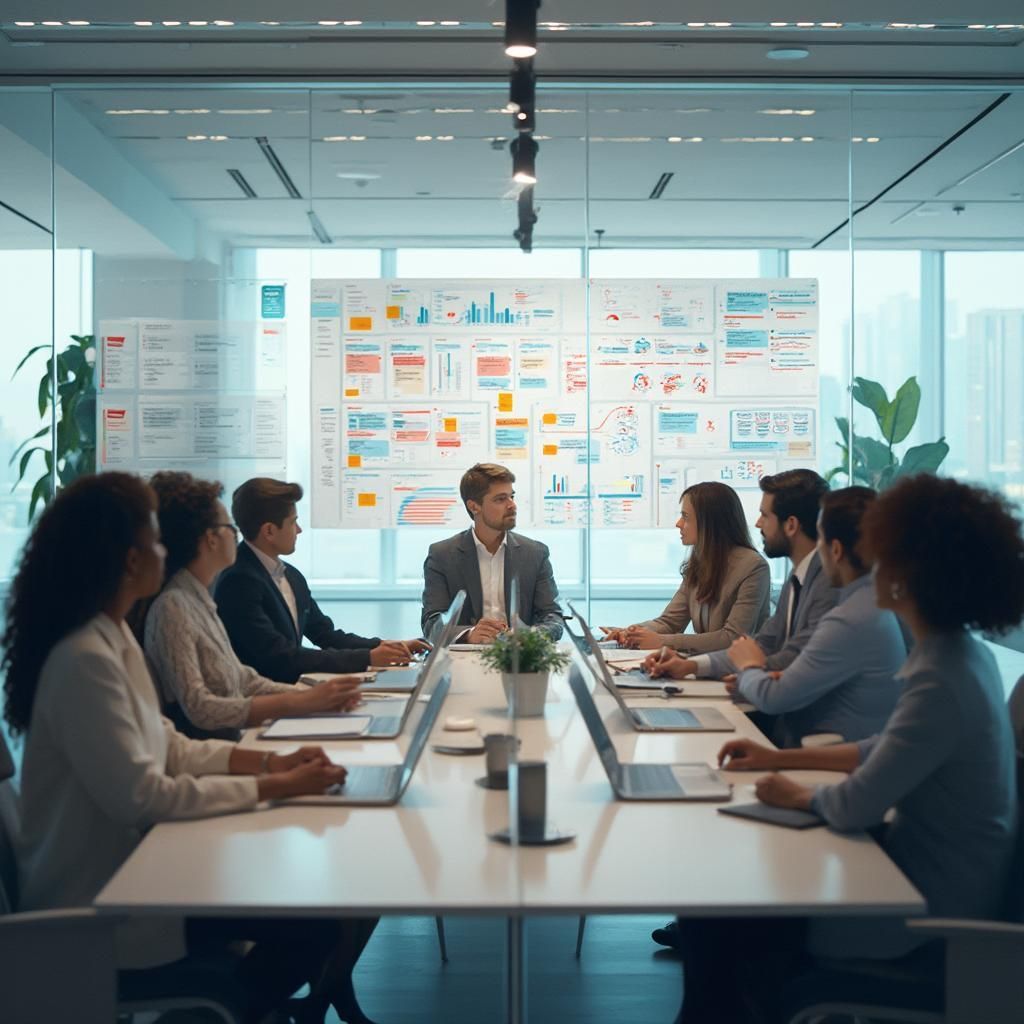
Investment Strategies & Budget Control
Read More
Smart Investment & Budget Optimization
We help businesses make informed investment decisions and maintain effective budget control. Our strategies are designed to allocate resources efficiently, reduce unnecessary expenses, and ensure financial stability while maximizing growth potential.
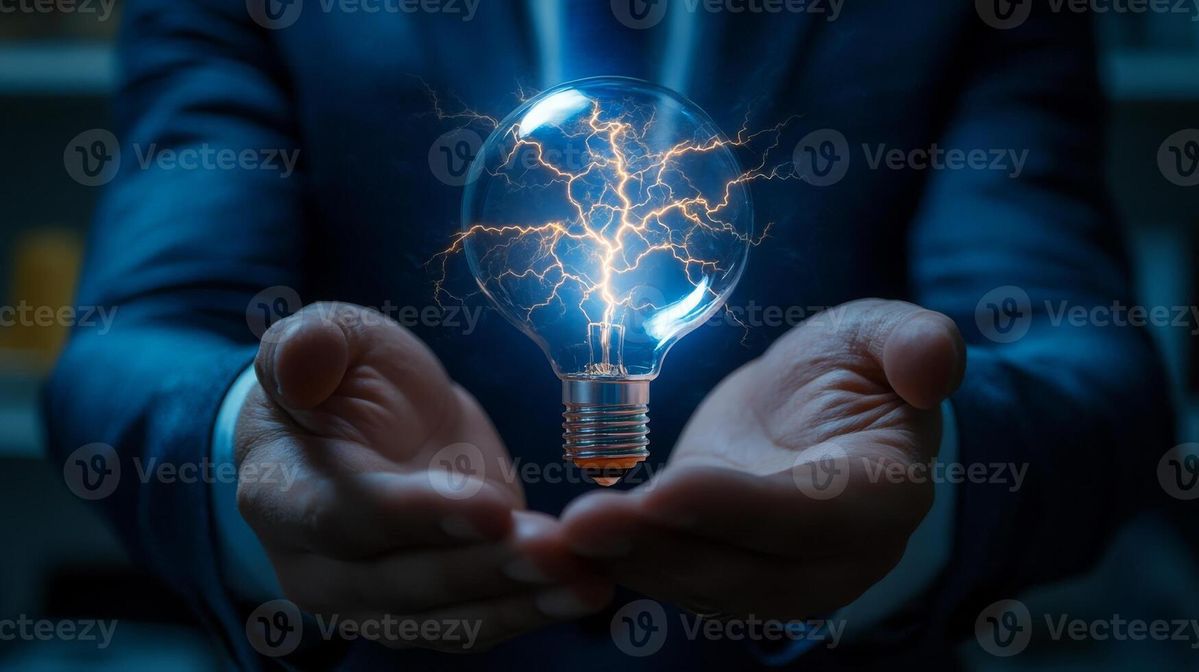
Tax Optimization & ROI Analytics
Read More
Tax Efficiency & Performance Analytics
We assist businesses in minimizing tax liabilities through strategic planning and compliance, while leveraging ROI analytics to measure financial performance. Our solutions ensure maximum profitability, transparency, and informed decision-making across all levels of the organization.
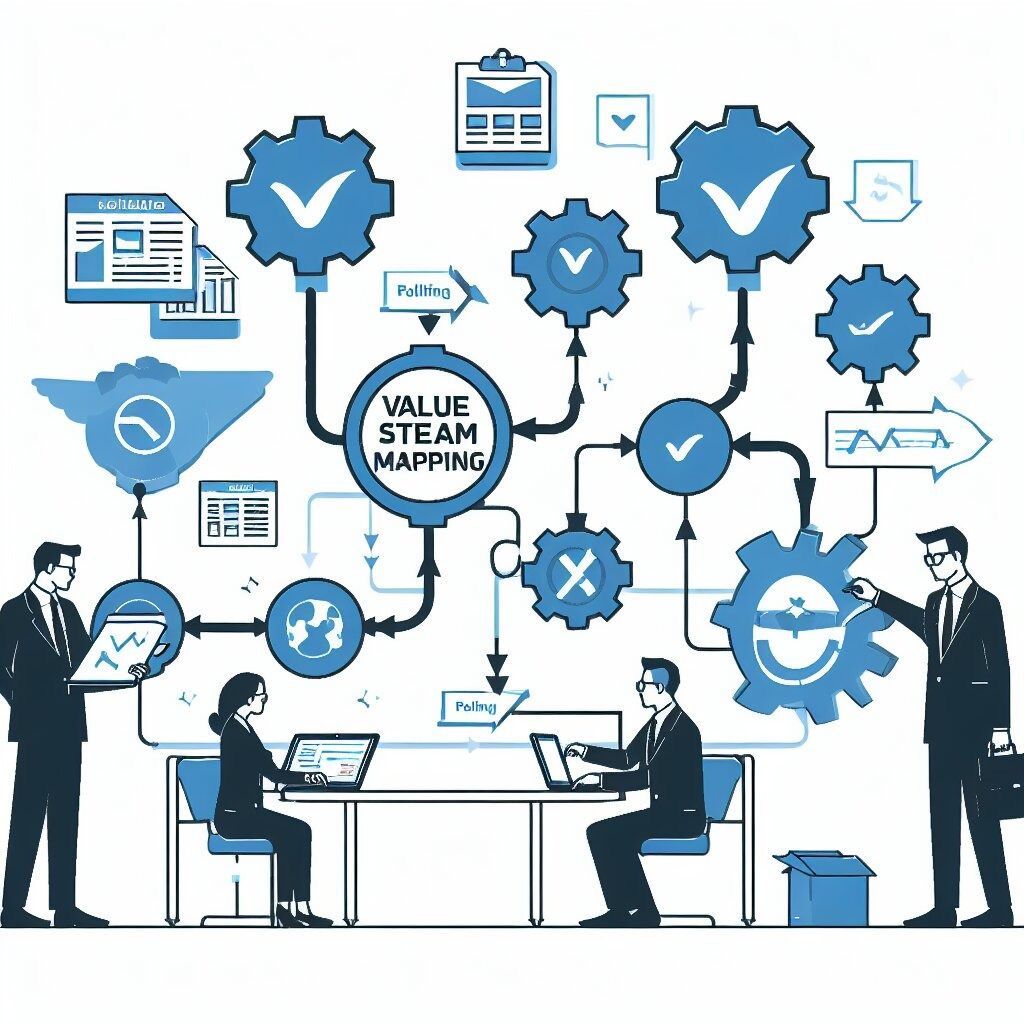
Value Stream and Mapping
Read More
Highlighting areas for cost and time savings in end-to-end workflows.
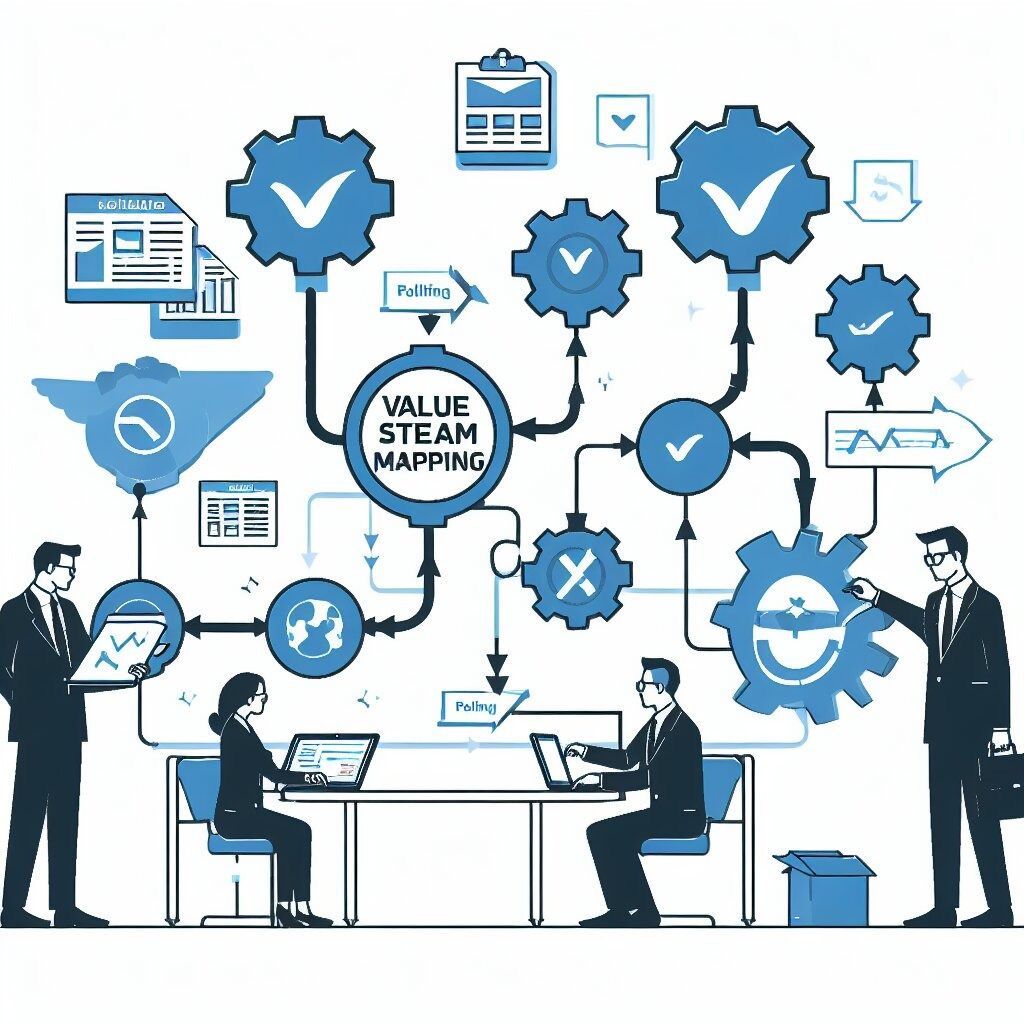
Value Stream and Mapping
Read More
Value stream mapping is a strategic tool used to analyze and improve the flow of materials and information through a production process. By visually mapping out the entire value stream, from raw material intake to finished product delivery, organizations can identify areas where value is being added and, more importantly, where waste is occurring. This includes inefficiencies such as delays, excessive movement, overproduction, or unnecessary inventory. The value stream map highlights the current state of operations and serves as a foundation for designing an optimized future state, with the goal of improving process efficiency, reducing lead times, and enhancing customer value. By using value stream mapping, companies can streamline their processes, eliminate bottlenecks, and ensure a smoother, more effective production workflow.
bussiness
OperationalRisk Management
"Mitigating Threats and Ensuring Business Continuity through Effective Risk Management"
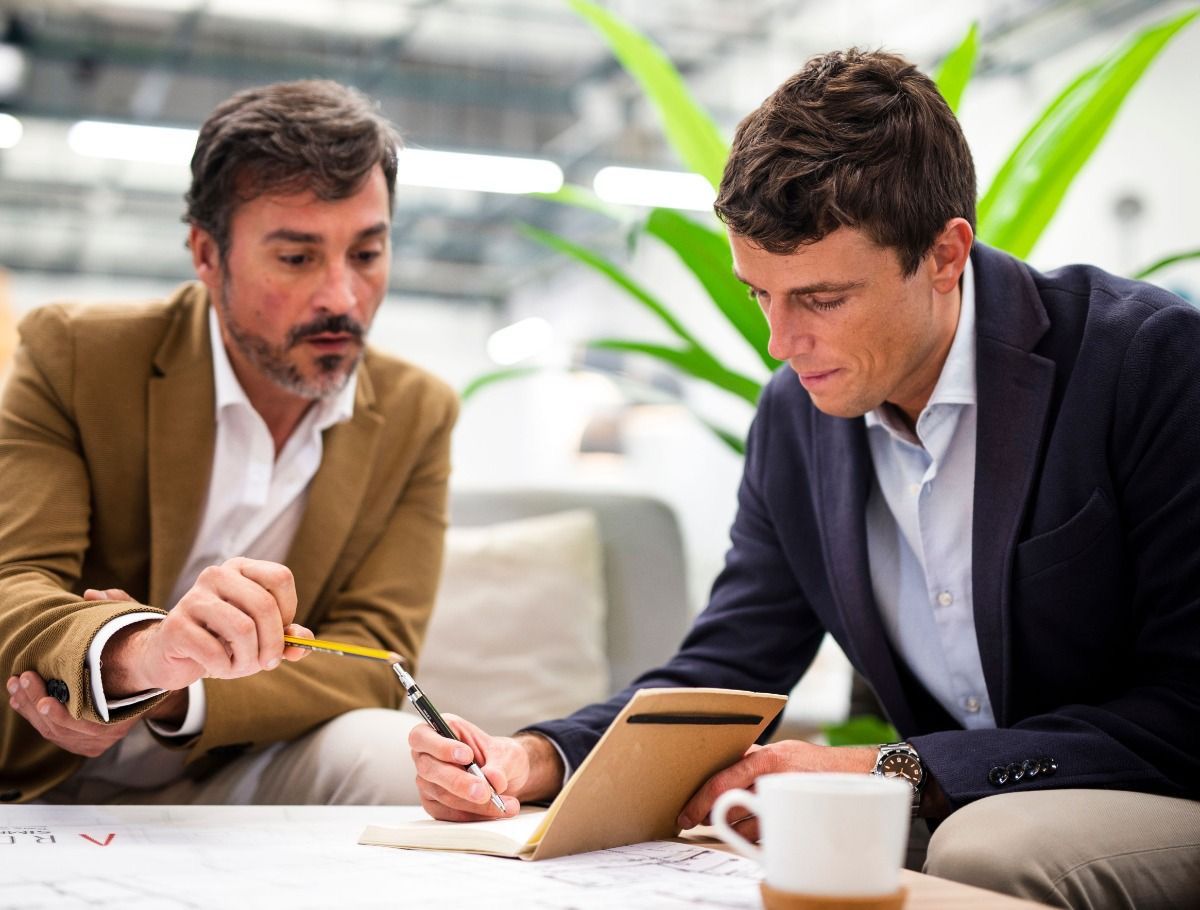
Business Continuity Planning
Read More
Business continuity planning (BCP) is a proactive strategy that ensures an organization can maintain essential operations during and after disruptive events, such as natural disasters, cyber-attacks, or other unforeseen crises. It involves identifying critical business functions, assessing potential risks, and developing detailed plans to minimize downtime and recover quickly. Key components of a BCP include disaster recovery strategies, communication plans, backup systems, and employee training. By preparing for potential disruptions, businesses can safeguard their operations, protect their reputation, and minimize financial losses. A well-executed business continuity plan enables organizations to remain resilient and maintain service continuity, even in the face of adversity.
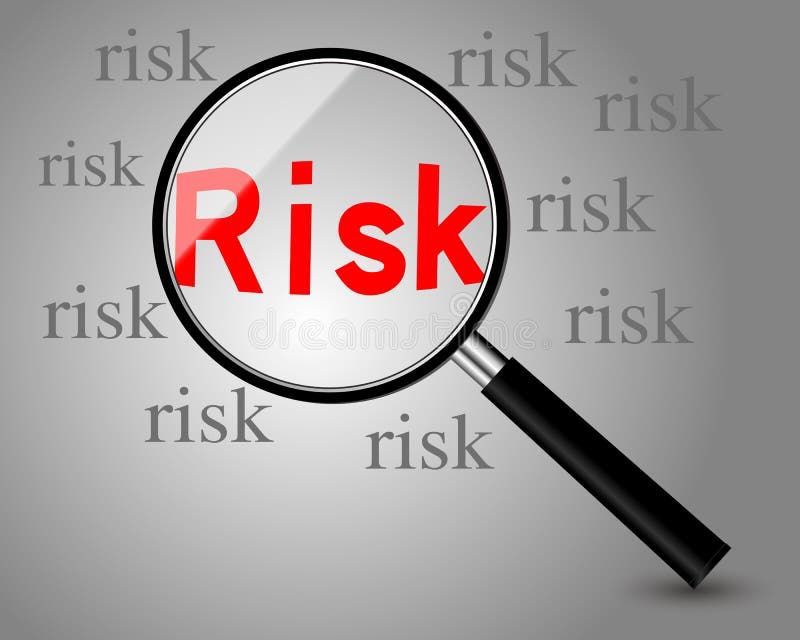
Risk Identification Frameworks
Read More
Risk identification frameworks are structured tools and methodologies designed to help organizations systematically identify, assess, and prioritize risks that could affect their operations or objectives. These frameworks typically involve gathering input from various stakeholders, analyzing potential threats, and evaluating the likelihood and impact of each risk. By using techniques such as risk mapping, SWOT analysis, or risk matrices, businesses can gain a comprehensive understanding of both internal and external risks. Once identified, risks are categorized and prioritized based on their severity, enabling organizations to focus resources on managing the most critical threats. A well-established risk identification framework helps businesses proactively address vulnerabilities, ensuring better risk mitigation and informed decision-making.
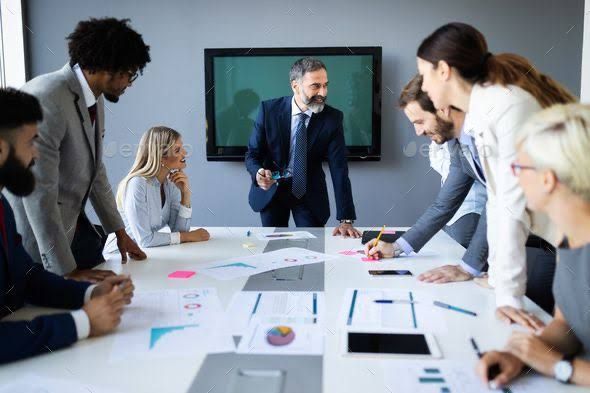
Crisis Management Strategies
Read More
Crisis management strategies are comprehensive plans designed to enable organizations to respond quickly and effectively to critical situations, minimizing damage and ensuring continuity. These strategies involve pre-established protocols, communication plans, and designated crisis management teams to address emergencies such as natural disasters, data breaches, or reputational crises. By preparing for potential crises in advance, organizations can act swiftly, provide clear guidance to employees and stakeholders, and make informed decisions to mitigate the impact. Effective crisis management not only helps to protect the organization’s assets and reputation but also builds trust with customers, employees, and the public, ensuring a quicker recovery and long-term resilience.
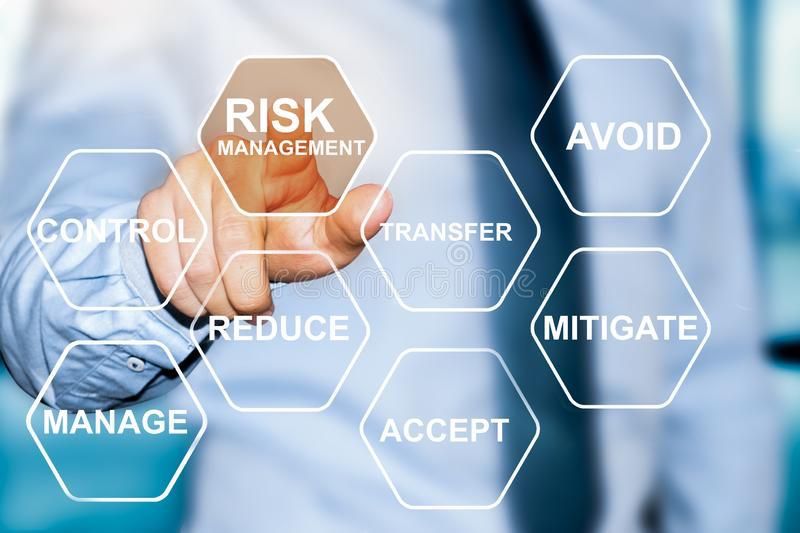
Operational Risk Training
Read More
Operational risk training is designed to equip teams with the knowledge and skills needed to identify, assess, and mitigate risks in day-to-day operations. This training ensures that employees at all levels understand potential threats to business continuity, from process inefficiencies to external factors like regulatory changes or cyber threats. Through case studies, simulations, and hands-on exercises, teams learn how to recognize risks early, implement preventative measures, and respond effectively when issues arise. By fostering a proactive risk management culture, operational risk training helps reduce the likelihood of disruptions, enhances decision-making, and ultimately ensures smoother, more resilient operations across the organization.
bussiness
Indhustry(4.0) and Automation
"Revolutionizing Production: Embracing Industry 4.0 and Automation for Enhanced Efficiency"

IoT Integration
Read More
IoT (Internet of Things) integration involves connecting physical devices, machines, and systems to the internet, allowing them to collect and exchange data in real-time. By embedding sensors and communication technologies into everyday objects, IoT integration enables businesses to monitor operations, track assets, and gather valuable insights for decision-making. In industries like manufacturing, healthcare, and logistics, IoT integration enhances efficiency by automating processes, predicting maintenance needs, and improving resource management. This interconnected ecosystem helps companies optimize performance, reduce operational costs, and deliver more personalized experiences to customers. Ultimately, IoT integration drives innovation, increases agility, and enables businesses to stay competitive in a rapidly evolving digital world.
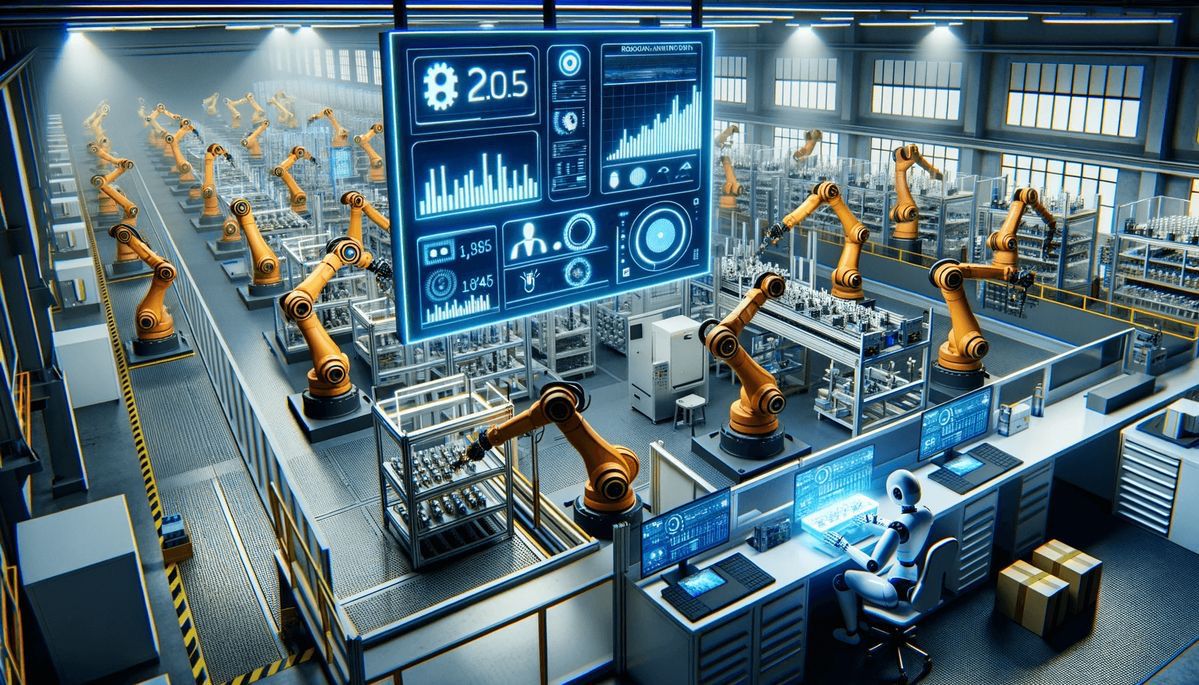
Robotic Process Automation
Read More
Robotic Process Automation (RPA) is a technology that uses software robots or "bots" to automate repetitive, rule-based tasks traditionally performed by humans. These tasks can include data entry, invoice processing, customer support, and more. By implementing RPA, businesses can streamline operations, reduce human error, and increase efficiency. RPA can work across multiple systems without the need for complex integrations, making it a cost-effective solution for automating high-volume processes. This automation not only frees up employees to focus on more strategic and value-added activities but also enhances overall productivity and accuracy, driving faster decision-making and operational agility in the organization.
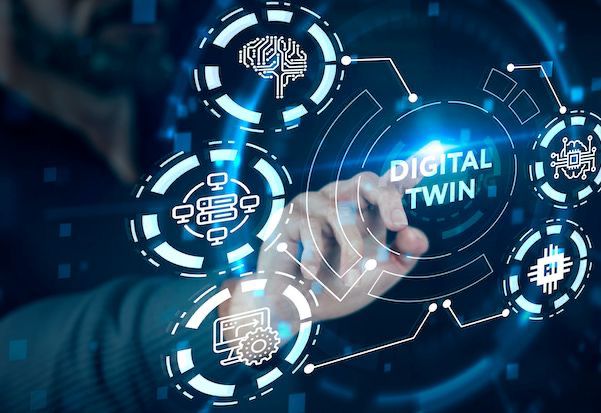
Digital Twin Technology
Read More
Digital twin technology involves creating a virtual replica of a physical object, system, or process, allowing businesses to simulate and monitor real-world conditions in real-time. By using sensors and data analytics, digital twins capture data from physical assets and translate it into a digital model, enabling continuous monitoring, analysis, and optimization. This technology is particularly valuable for industries like manufacturing, healthcare, and urban planning, where it helps improve operational efficiency, predict maintenance needs, and streamline decision-making. Digital twins provide a deeper understanding of performance and allow for proactive problem-solving, reducing costs and enhancing productivity while also supporting innovation and long-term planning.
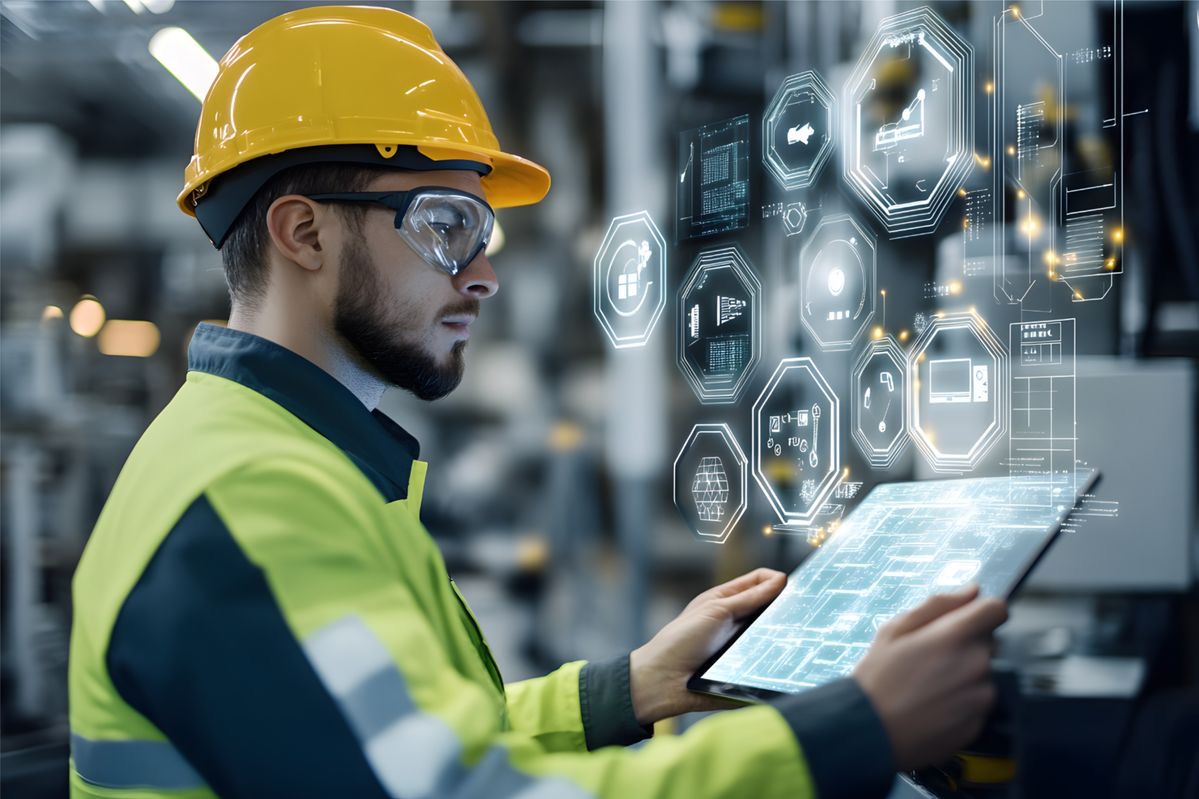
Smart Factory Implementation
Read More
Smart factory implementation involves integrating cutting-edge technologies like the Internet of Things (IoT), automation, robotics, artificial intelligence (AI), and data analytics into manufacturing operations to create a more connected, efficient, and adaptive production environment. By enabling machines, systems, and sensors to communicate in real-time, smart factories provide valuable insights into production processes, helping businesses optimize performance, reduce downtime, and enhance product quality. These innovations enable predictive maintenance, supply chain improvements, and faster responses to changing market demands. Implementing a smart factory not only increases operational efficiency but also supports sustainability, innovation, and long-term competitiveness, positioning businesses for success in an increasingly digital industrial landscape.
For Enquiry
Focus Technologies is a global consulting firm specializing in Operational Excellence, R&D, and cutting-edge business solutions, empowering organizations with innovative training, digital transformation, and strategic growth.